Insulating Sleeves
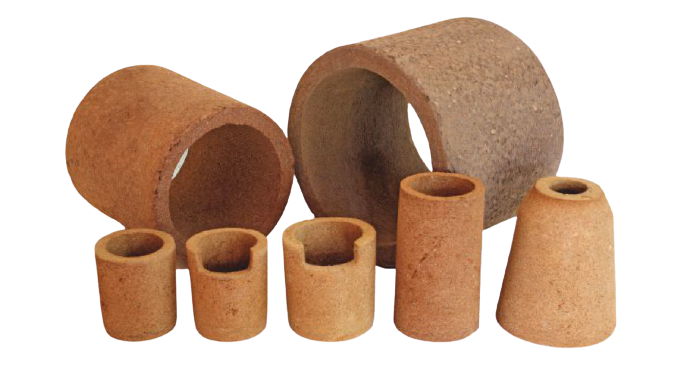

Insupour Sleeves (Insulating Sleeves)
Insupour & Exopour is a range of exothermic and insulating sleeves. These sleeves are used to ensure proper feeding of the castings while reducing the size of the sand riser.
criteria for selection of the grade of sleeves
- Greater the exothermic action of sleeve poured metal in the riser will remain liquid for a longer time for perfect feeding and will also increase yield. For smaller castings, exothermic sleeves are recommended.
- Smaller the size of riser, more exothermic it should be. As the size of riser becomes larger, viz. diameter over 6″, insulating properties attain importance. Hence for large risers, insulating sleeves are recommended.
Available Grades Of Sleeve
SLEEVES GRADE
M.E.F
NATURE
FEEDING EFFICIENCY
METAL
INSUPOUR 1400
1.4
Insulating
20 – 22%
CI/SG, Non-Ferrous Alloys
INSUPOUR 140
1.5
Super Insulating
25 – 27%
Steel, SG Iron, Non-Ferrous Alloys
EXOPOUR 1600
1.6
Exothermic
25 – 27%
Steel
Note Feeding Efficiency This is an approximate indicator and should be interpreted as the approximate size by which the sleeve will be smaller than an equivalent sand riser.
Modulus Extension Factor (M.E.F.) =
- Solidification time for riser with sleeve
- Solidification time for sand riser (without sleeve)
Insupour 140 System is a combination of Ceramic Foam Filter & Insulating Sleeve. It is used for Cast Iron, Aluminium, Copper Base alloys & Steel.
Insupour Mechanism takes place in two stages, viz. FILTRATION AND FEEDING.
Filtration
The filtration effect is due to the mechanical entrapment of inclusions. The change in flow and pressure through the filter causes the contaminants (Inclusions) to stick to the filter labyrinth (web of the pore). Our Filters have maximum open pore structure (minimum internal blockages) which result in the following benefits:
- Enhances the filtration efficiency & flow rate.
- Reduces entrapment of air bubbles into the metal downstream.
- Changes Turbulent flow to a Laminar flow.
- Reduces the oxide formation within the filter.
Feeding
Once Filtration takes place Ceramic Foam Filter floats at the top & Feeding action starts. The feeding effect is due to the highly Insulating nature of the Sleeve. It improves the temperature gradients within the castings & promotes the Directional Solidification.
Salient Features Of Insupour System
- The gating system is completely eliminated.
- Rejection due to slag inclusion especially at the machining stage is minimized.
- The soundness of Casting is improved.
- Fettling work & other rework is minimized.
- The surface finish of casting is improved.
- Machinability is improved.