COALBOND POWDER
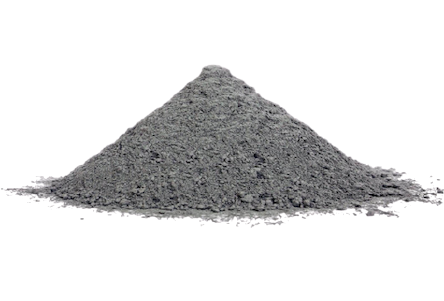
Coalbond Powder (For Green Sand Mold Practice)
CoalBond powder generates higher amount of lustrous carbon than coal dust. Hence better casting finish is observed consistently even with addition as low as 0.25% – 0.4% on sand (Lustrous carbon in CoalBond is nearly 7 times more than coal dust).
characteristics and features
CoalBond Powder is finding increasing application in progressive foundries as a substitute for coal dust powder in green sand moulding for gray malleable & S.G. Iron castings. It is a unique synthetic product manufactured under controlled parameters using quality raw materials.
Grades of Coalbond Powder
GRADE
ASH CONTENT
VOLATILE MATTER
CoalBond 70
3.0 % Max.
70%
CoalBond 65
6.0 % Max.
60%
advantages of coalbond powder over coal dust
1. Better Casting Finish: CoalBond powder generates higher amount of lustrous carbon than coal dust. Hence better casting finish is observed consistently even with addition as low as 0.25% – 0.4% on sand (Lustrous carbon in CoalBond is nearly 7 times more than coal dust). Higher percentage of lustrous carbon in CoalBond, allows lower percentage addition in sand.
2. Lower & consistent ash content: Hence better refractoriness of sand and lower sand fusion. So foundries can use higher percentage of return sand. i.e. lower % of new sand, resulting in overall cost reduction.
3. Unlike coal dust, CoalBond has no auto ignition tendency.
4. Foundries get higher permeability & lower ash built up in the sand resulting into lowering dead clay and increased cycles of return sand.
5. Unlike coal dust CoalBond does not absorb moisture hence lower moisture addition is required to get Temper bond/Green strength. This minimizes the chances of blowholes in castings.
6. Reduces metal penetration and gives sharp corners.
7. Acts as excellent anti-scabbing agent.
8. Improves sand flow-ability and texture, hence can be used even in automated sand plants.
9. Does not produce air-borne dust particles. Thereby keeping air in the foundry clean.
method of using
- Product application should be started with 1%* by weight with return sand to new sand ratio of 80:20
- From 1%* it has to be reduced gradually and stabilized to 0.25% – 0.4%*
- From our practical experience and trials conducted at various foundries we recommend following procedure for its application.
- Stop use of coal dust completely and start use of 1%* CoalBond.
- Keep return sand 80% and new sand 20%. This will flush out the coal dust in the system.
- Subsequently reduce CoalBond addition by 0.20% – 0.25% for next five (5) cycles and finally stabilize on 0.25% – 0.4%*.
Note:
Practices vary from foundry to foundry. Each foundry will have its own judgment to stabilize the lowest percentage of addition. However, the ingenuity of the foundry-man and ability to improvise in a given set of circumstances has shown that applications are not limited to these suggestions alone.
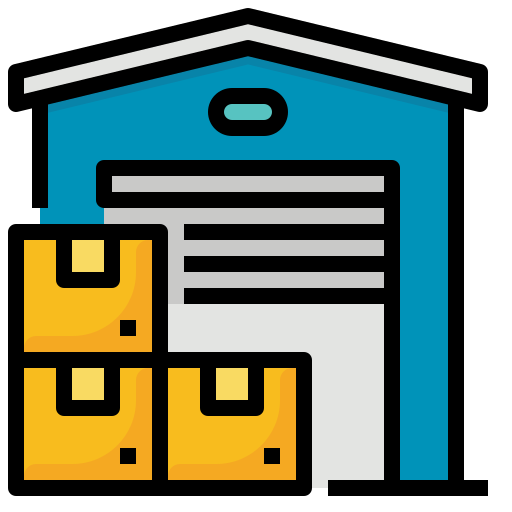
Storage
Store in a dry place

Shelf Life
6 months from the date of manufacture.
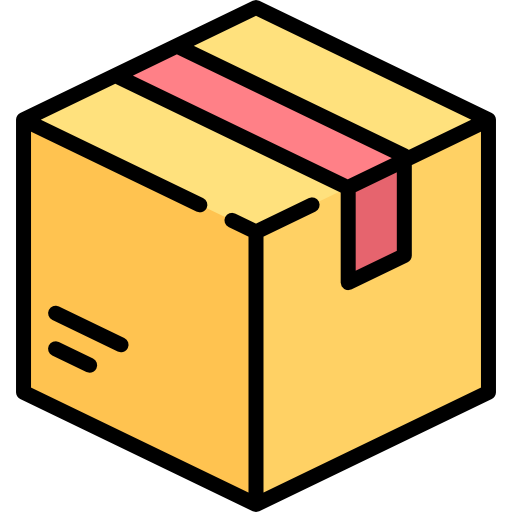
Packing
40 kg in arkalline bags.